Assembly Track Tasks
The assembly track of the challenge uses an extended MuJoCo4 environment with ROS integration. The assembly environments provide a ros_control interface to send position, velocity, or effort commands to the robot. Furthermore, joint position and velocity as well as force/torque sensor readings of the end-effector are accessible via ROS topics. For visual processing, a fixed RGB-D camera facing the workspace and a hand-mounted RGB camera will be available. The track is split into a screwing and a plugging task and both will be offered with multiple levels of difficulty.
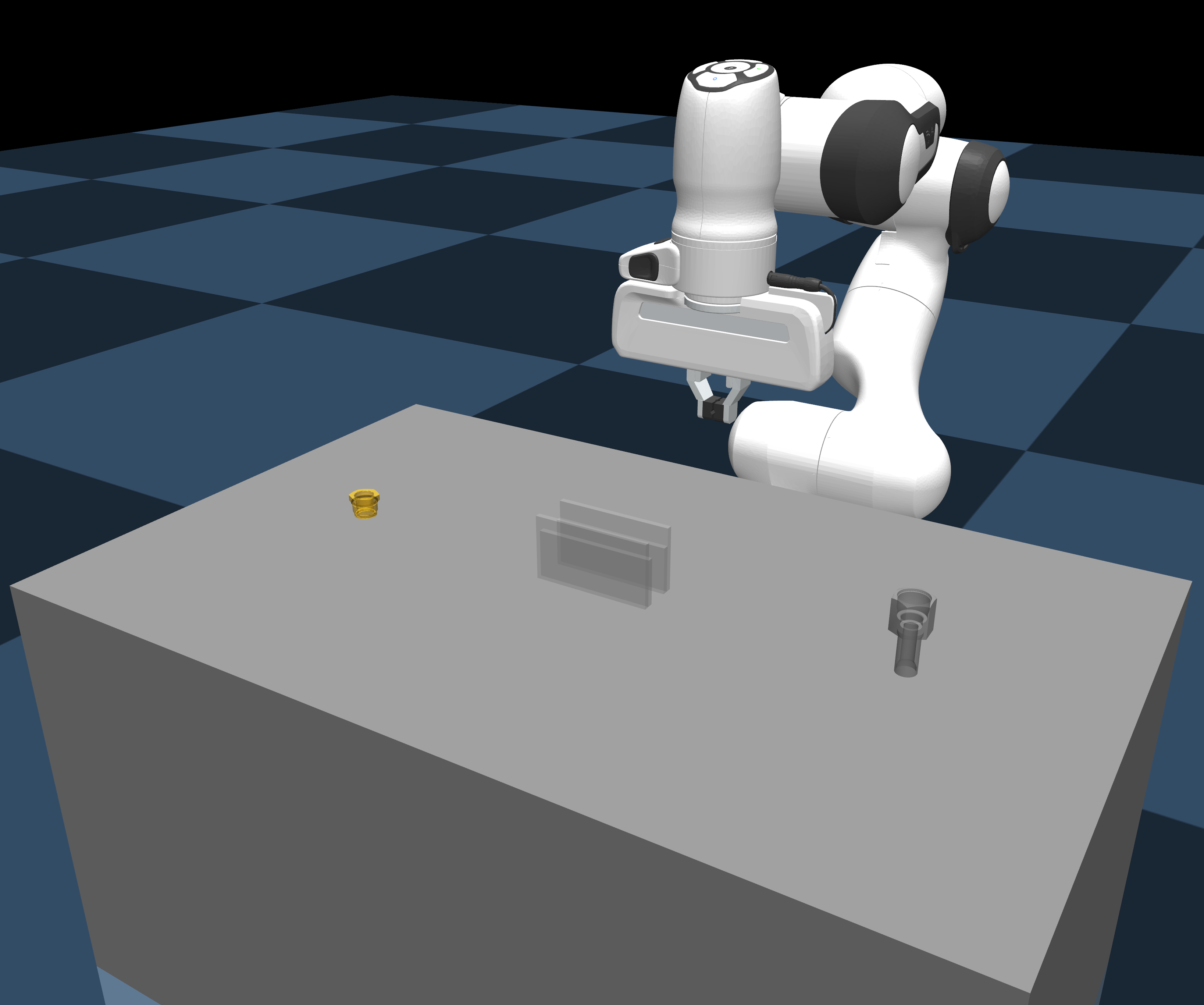
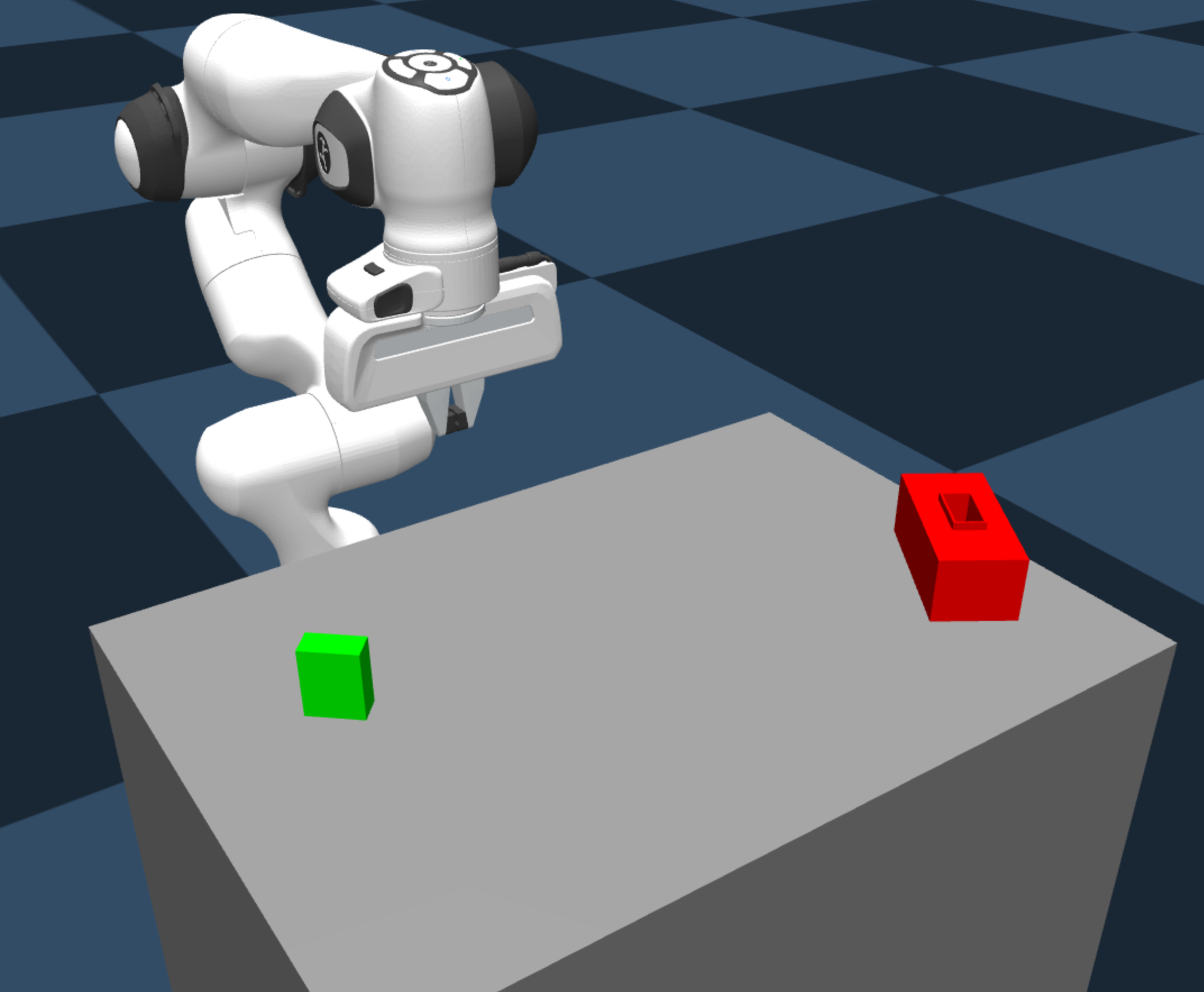
Screwing
For this task, a screw, a nut, and a fixture are placed on the workspace table – their object meshes will be available. The goal is to thread the screw into the nut. This requires solving the following sub tasks: pick up the nut, place the nut into the fixture, pick up the screw, align screw into nut, and tighten the screw. Each sub task should be completed within 5 minutes, otherwise the whole run will be terminated prematurely.
Plugging
For this task, a peg-like plug and its counterpart, a frame with a hole, are placed randomly on the workspace table. The object meshes will be available to participants again. Additionally, the Cartesian poses of the plug and the frame will be observable from the environment. However, the frame’s actual pose will be perturbed along the table’s surface by a random sample from a given uniform distribution, depending on the difficulty level. The goal is to pick the plug and insert it into the frame against a clipping force profile, which requires solving the following sub tasks: pick up the plug, localize the frame, align plug into frame, and click-insert the plug. Each sub task must be completed within 30 seconds, otherwise the whole run will be terminated prematurely during evaluation.